Посещение фабрики Hope - там, где рождаются HB.160
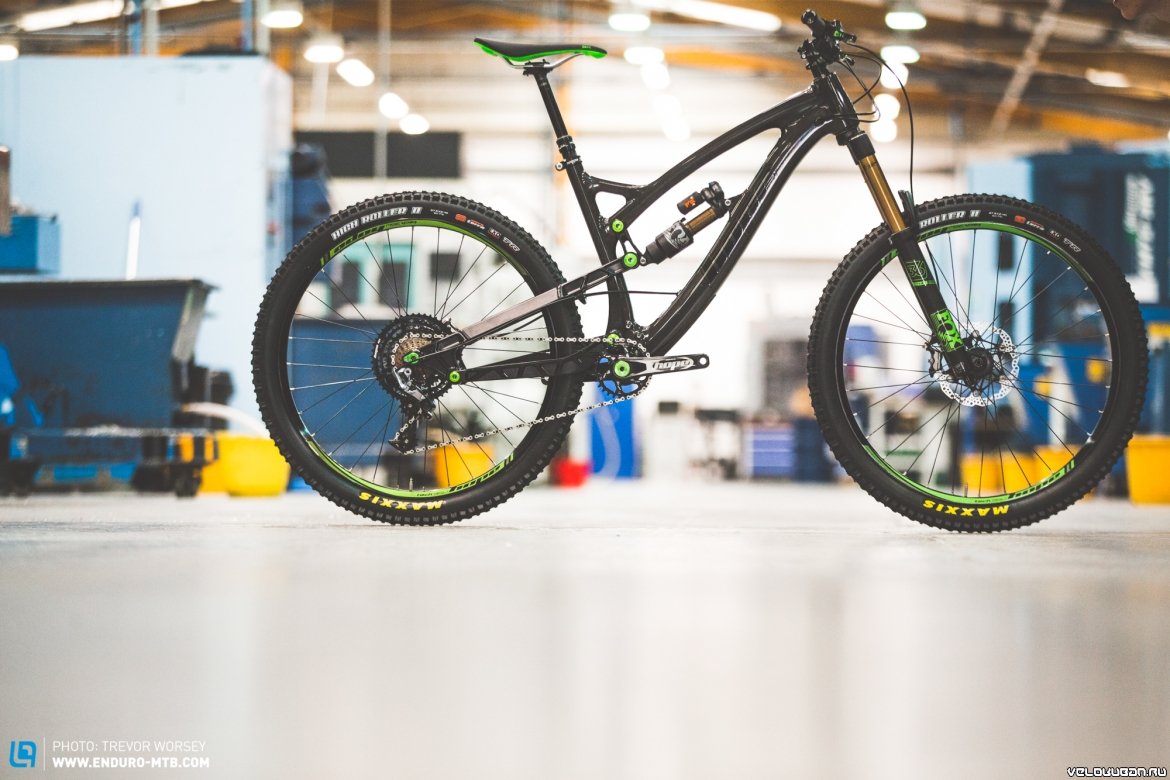
Перед нами предстал большой массивный стол, на котором лежит огромный алюминиевый саркофаг. Один за другим толстые крепежные болты отвинчиваются и осторожно вытаскиваются из его крышки. После приложенного усилия на специальный рычаг, две половины саркофага отделяются друг от друга, и мы все почему-то отступаем, задержав дыхание. Словно из раскрывшейся раковины моллюска, из саркофага, появляется на свет жемчужина - рама с гладкими, полированными формами из идеального шевронного плетения углеродного волокна, в котором ярко отражаются огни люминесцентных ламп. Так рождается новый Hope HB.160.
«Меня зовут Д'Арт, как мушкетера Д'Артаньяна, потому что у меня была готичная борода. Это немного раздражает, так как он даже не настоящий мушкетер.»
Крис умело раскладывает предварительно разрезанные листы из углеродной ткани в форму для HB.160. Как гигантская головоломка, велосипед медленно формируется по одному листу за раз.
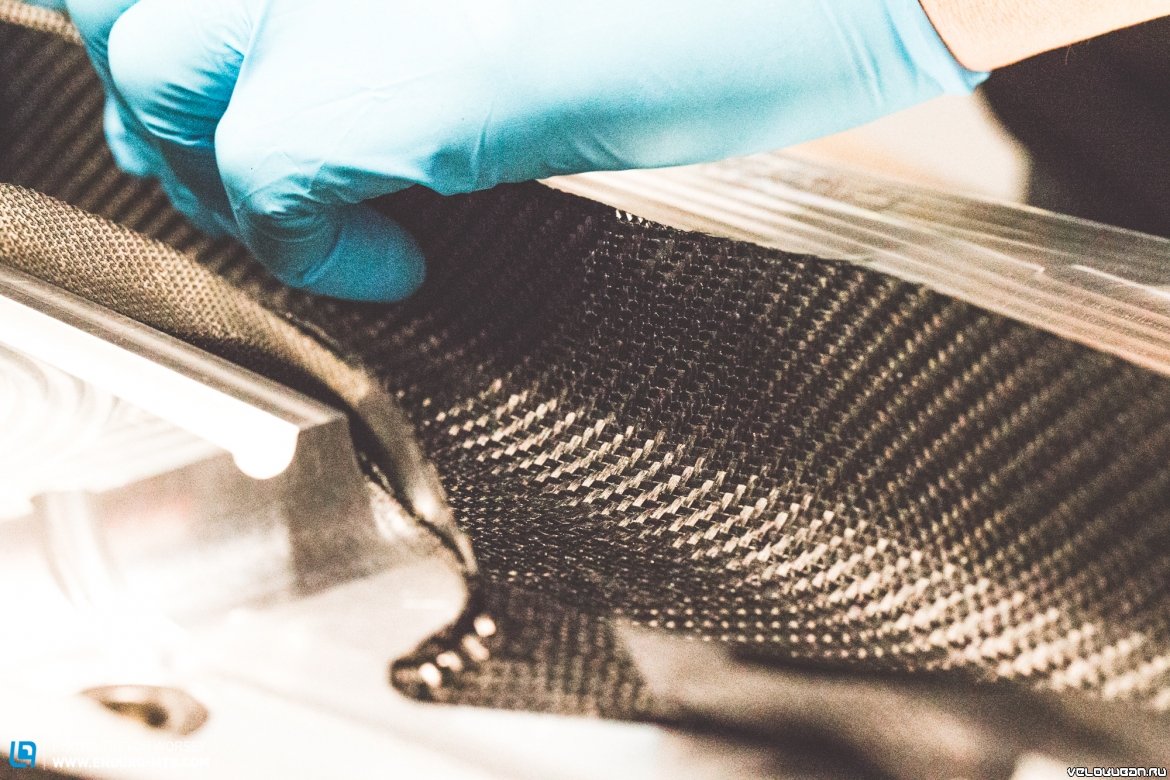
«Последний пролет, который мы видим сейчас, стал таким после многих прототипов. Ранние передние треугольники весили более 1,2 кг, но после многочисленных тестов они были серьёзно переработаны - после тщательной реорганизации, рама была оптимизирована до 900 г без потери прочности»
Теперь любой может производить алюминиевые или стальные велосипеды с помощью сварщика и некоторых навыков работы с металлическими изделиями. А вот для карбоновой версия рамы, нужна пресс-форма, вырезанная из куска алюминия размером с журнальный столик. Форма представляет собой сердцевину для HB.160 и она не дешевая - каждая её половина вытачивается на огромной машине с ЧПУ четверо суток. Когда мы шли по фабричному этажу, мы некоторое время наблюдали, как обрабатывается новая форма небольшого размера. Координаты резки вспыхивают один за другим на цифровом экране, и я замечаю, что линия проходит 60 000 точек.
«Как много координат», - говорю я. «О, это всего лишь секция около дропаута», - объясняет машинист.
Огромная машина с ЧПУ часто останавливается, принимая очередную партию инструкций, прежде чем снова зажужжать и начать резать. Неудивительно, что производство формы может стоить более 100 000 евро. Умножьте это на несколько разных размеров, и вы сможете понять, насколько дорогим может быть тёмное искусство углеродного волокна. Конечно, Hope может изготовить собственные формы, что является огромным преимуществом в таком конкурентном секторе.
Это все конечно очень интересно, но вернёмся в «Углеродную комнату». Начиная с декоративного верхнего листа, Крис мягко сглаживает свое секретное сочетание карбоновых полотен и однонаправленных волокон. Каждый предварительно отрезанный лист помещается точно на своё место, предварительно пропитываемый смолой. Трудно представить, что нечто настолько мягкое и прекрасное можно превратить в настолько прочную структуру. Как только Крис заканчивает, все проверяется и перепроверяется, добавляются внутренние камеры, а тяжелая форма поднимается и затем закрывается.
Все помогают катить колесный стол по мастерской до гигантского пресса - вот где творится настоящая алхимия. Болты размером с кулак завинчиваются в свои отверстия, и начинается трансформация.
В течение трех часов форма томится в печи при 120°С под давлением в двенадцать тонн. Вследствие этого смолы затвердевает и из карбонового полотна рождается прочный каркас рамы.
Освобожденная из формы рама попадает под опытный глаз Нила. На рабочем столе он аккуратно обрабатывает раму наждачной бумагой, от 180й и до 500й, тщательно удаляя излишки смолы и крошечные участки перелива из формы.
Беру раму в руки - прекрасное творение из углерода, хотя ещё тусклое и не покрытое прозрачным лаком, всё равно отсвечивает свет флуоресцентных ламп.
Каждая рама, которая выходит из форм, собирает толпу - вся команда тщательно проверяет каждое волокно, чтобы обеспечить абсолютное совершенство.
После шлифования рулевая и чашки каретки аккуратно монтируются на свои места. Затем раму подвешивают и в течение семи дней она полностью затвердевает.
Скрепляющая карбон смола невероятно прочна. На самом деле она прочнее, чем материал, который она связывает: после 600 000 циклов сжатия ни один сегмент рамы не дал трещины или расслоения материала.
«Возможно, нам нужно делать велосипеды из одной смолы!» - шутит Нил.
Несмотря на то, что идея велосипеда от Hope обсуждалась в компании достаточно долго, геометрии байка была найдена довольно быстро. На самом деле, четвертый велосипед вышедший из формы жёстко испытывают и по сей день. Этот велосипед гоняют вокруг завода и в хвост и в гриву в течение нескольких месяцев, и никто не уверен, что ещё можно с ним сделать. Но сколько лет он прослужит? Как будет использоваться? Однажды кто-то выехал на нём на улицу по ступеням парадного входа, а затем спрыгнул со стены - кароч сорвал ему целку!)) Затем десяток сотрудников направились прямо к склонам Йоркшира и по очереди драли его по полной, гоняя на нём с холма. Перья этого памятного байка по-прежнему покрыты шрамами после его первого дня жесткача. У Hope был собственный велосипед, и он был хорош.
У Hope наконец есть свой велосипед. То, что начиналось как мечта основателей Иана Вейтрила и покойного Саймона Шарпа, построить велосипед для семьи Hope, теперь стало реальностью. И это реальность теперь доступна их поклонникам, покупающим пятьсот велосипедов в год. Норе не собирались продавать велосипеды, они просто хотели посмотреть, смогут ли они изготовить по настоящему надежный и элегантный велосипед, который год от года будет "солдатом", побеждающим всё, от альпийских спусков, до самой жесткой йоркширской гравийки. Это настоящая алхимия, а приготовлена она ребятами в кроссовках Five Ten, предпочитающими памп трек на обед.
P.S. Понравился материал - жми палец вверх, не понравился - не жми. Ваша активность даёт заряд авторам на написание новых статей!